The Technologies That Could Finally Make Space Elevators a Reality
Thanks to recent advances in materials science, Space Elevators have become somewhat feasible at last.
Like the Stanford Torus, the O'Neill Cylinder, and the Generation Ship, the Space Elevator is one of those ideas that keep popping up! Just when you think scientists and engineers have given up on it, there's a new round of theoretical studies that assert how it could be done. You might say that the Space Elevator is an idea that's too good to let go of.
Considering the benefits involved, this should come as no surprise. Granted, the cost in terms of money, resources, and time would be considerable, as are the engineering and logistical challenges involved. But for the one-time price of creating this megastructure, we would be able to realize space-based solar power, habitats in orbit, cities on the Moon and Mars, and more!
It would be no exaggeration at all to say that a Space Elevator would allow humanity to "build a road to space" (as Jeff Bezos says) or become "an interplanetary species" (as Elon Musk says). Basically, any and all plans for harnessing the resources of space, saving Earth from climate change, and settling all across the Solar System could be much easier to realize.
In a previous article, we took a look at the history of the concept, the many studies that have been conducted, and the handful of attempts that have been made. However, there have been considerable developments in recent years that merit attention all on their own. And the exciting thing is, they just might lead to a Space Elevator in our lifetime.
A brief history
Like most revolutionary ideas for space exploration that have stood the test of time, the Space Elevator can be traced to Russian/Soviet rocket scientist Konstantin Tsiolkovsky (1857-1935). Known as one of the "founding fathers" of rocketry and astronautics, Tsiolkovsky is credited with the formulation of the "Rocket Equation" and the basic design from which most modern rockets are derived.
Other proposals made by Tsiolkovsky included rockets with steering thrusters, multistage boosters, rotating pinwheel space stations (which would simulate gravity), airlocks, and closed-cycle systems to provide food and oxygen for space habitats. In addition, he also conceived of a structure that reached all the way to geostationary orbit (GSO), or an altitude of 22,236 mi (35,786 km).
However, Tsiolkovsky's version of the idea called for a compression structure, which was inspired by his visit to Paris in 1895, where he witnessed the Eiffel Tower for the first time. Tsiolkovsky himself noted that this was an unrealistic idea since no known material was strong enough to support its own weight when standing so tall.
In 1959, Soviet engineer Yuri Artsutanov proposed a more practical version of the idea (what he called an "Electric Train to the Cosmos") by suggesting that a station be deployed in GSO and a tension structure be deployed downward. This "tether" would connect the station to the surface and allow for payloads to be lifted into orbit using very little energy compared to conventional rockets.
This same concept was proposed by four American engineers in 1966, who independently came to the same conclusions regarding a suspension structure. Their version of the reinvented concept was known as a "Sky-Hook," which popularized the idea among aerospace engineers and scientists in the United States.
In all cases, the design called for a megastructure consisting of a base (or "Anchor") attached to a mobile platform at sea or a stationary one on land. A suspended cable (or Tether) would connect the base to a Counterweight in space, which could be a captured asteroid or a spaceport positioned beyond GSO (or a combination thereof).
Delivering payloads and people to and from space would be a series of Climbers (or cable cars), the design of which would vary based on the number of cars deployed on the tether and the design of the tether itself. These cars would be powered by means of solar panels, nuclear reactors, and wireless or direct energy transfer.
Alas, the same problem that stumped Tsiolkovsky would go on to stump proponents of suspension elevators for decades. No known material was ever strong enough to support an object in orbit.
The trouble with tethers
Until very recently, every theoretical study concerning Space Elevators always hit a wall when it came to the question of what material would be used to make the tether. In all cases, the tensile strength-to-weight ratio was never high enough to ensure that the structure wouldn't break under the strains placed on it by Earth's gravity and its rotation.
As Arthur C. Clarke summarized in his address to the 30th International Astronautical Congress (IAC) in 1979, titled "The Space Elevator: 'Thought Experiment, or Key to the Universe?'":
"How close are we to achieving this with known materials? Not very. The best steel wire could manage only a miserable 31 mi (50 km) or so of vertical suspension before it snapped under its own weight. The trouble with metals is that, though they are strong, they are also heavy; we want something that is both strong and light. This suggests that we should look at modern synthetic and composite materials. Kevlar... for example, could sustain a vertical length of 124 mi (200 km) before snapping - impressive, but still totally inadequate compared with the 3100 (5000) needed."
Based on various assessments, the material involved would need to have a strength of at least 100 gigapascals (GPa) to withstand the stresses involved. For comparison, A36 structural steel has a tensile strength of around 550 MPa, or roughly 1/180th the strength required. Throughout the latter half of the 20th century, no known material (natural or synthetic) was up to the task.
When he proposed his "Electric Train," Artsutanov theorized that the cable could be built from known synthetic materials, but which had only been produced in tiny quantities so far. The initial cable, he said, would measure one millimeter at the Earth's surface and extend to an altitude of 31,068 mi (50,000 km) (around 8,700 mi or 14,000 km beyond GSO).
This extra length would provide the additional mass needed to keep the whole system under tension. From there, Artsutanov proposed using the initial cable to multiply itself until 1000 cables were clustered together. He also proposed that the cable thickness be tapered, where it was thinner at ground level and thickest at GSO to make sure the stress remained constant.
In their "Sky-Hook" proposal, Isaacs et al. also proposed that the tether's thickness would need to be thinnest at the Earth (one five-hundredth of a centimeter) at taper outwards. They also briefly considered a number of materials — including quartz, graphite, beryllium, and even diamond — but determined that none were strong enough.
With the development of carbon nanotubes in the 1990s, there was revitalized interest in the concept. This led David Smitherman of the NASA Advanced Concepts Office (ACO) to propose that these materials could make a space elevator feasible. He presented these findings at the Advanced Space Infrastructure Workshop held at the Marshall Space Flight Center in June of 1999.
These were also published as a report in 2000 titled "Space Elevators: An Advanced Earth-Space Infrastructure for the New Millennium." According to Smitherman, the lightest and strongest materials that were readily available were graphite-epoxy composites, but carbon nanotubes (allowing for mass production) would be far better suited:
"If the space elevator was assumed to be a tapered, solid un1iform structure using the strongest composite materials available today (Spectra or PBO graphite-epoxy), the diameter at GEO would be 1.24 mi (2 km) and would taper down to 1 mm at the Earth's surface. The mass of the tethered structure would total approximately 60×10¹² tons. If carbon nanotubes can be made into continuous structural members, then the diameter at GEO would potentially be as small as 0.26 mm, 0.15 mm at the Earth's surface; and the total tether mass would be only 9.2 tons."
However, this was based on conservative estimates of the tensile strength required, which he claimed was roughly 62.5 GPa. Furthermore, his assessment of the strength of carbon nanotubes was rather optimistic, saying, "the actual strength of a carbon nanotube rope may be much higher than that."
This optimistic assessment was repeated by Bradley C. Edwards, who performed a feasibility study in 2000 with support from the NASA Institute for Advanced Concepts (NIAC). In his final report, titled "The Space Elevator," he offered the following assessment:
"[Carbon nanotubes] have the promise of being the strongest material yet discovered. This strength, combined with the material's low density, makes it critically important when considering the design of a space elevator. The tensile strength of carbon nanotubes has been theorized and simulated to be 130 GPa compared to steel at <5 GPa and Kevlar at 3.6 GPa. The density of the carbon nanotubes (1300 kg/m³) is also lower than either steel (7900 kg/m³) or Kevlar (1440 kg/m³)."
In 2003, Edwards followed up on this paper with the NIAC Phase II Final Report. Once again, he expressed optimism that a Space Elevator could be built using then-available technology and stressed that everything hinged on finding a suitable material for the tether and that carbon nanotubes were the best candidate.
Alas, when these reports were published, mass production was the major stumbling block for carbon nanotubes. Simply put, these structures are "grown," not machine-produced, and are limited in length. The current record for single-tube growth still stands at just under 20 inches (50 cm) and 5.5 inches (14 cm) for "forests" of them.
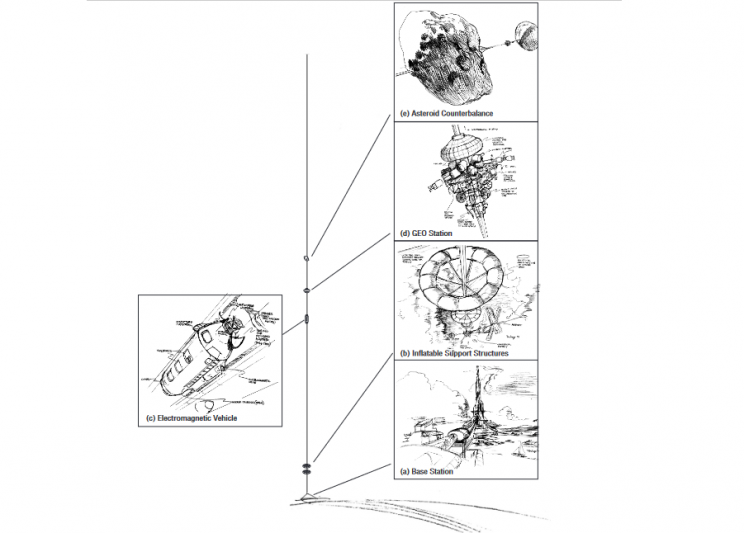
What's more, of those tubes that have been produced, their tensile strength has not measured up to theoretical or simulated results. Even worse, the hexagonal covalent bonds that give carbon nanotubes their high tensile strength also make them prone to fraying when placed under extreme stress.
The efforts to realize a Space Elevator effectively stalled at this point, roughly one year before graphene was isolated for the first time.
New materials
Because of the issue with carbon nanotubes, proponents of Space Elevators tended to move in one of two directions after 2003. On the one hand, some accepted that the material challenges would not be solved anytime soon and refocused their efforts on proposing elevators for other celestial bodies — the most notable being the Lunar Space Elevator.
Others placed their hopes on supermaterials that (until recently) were still in the theoretical stage. In recent years, many of these materials have moved from the theoretical to the production phase. Examples include nanodiamond filament and (more importantly) graphene.
Graphene is an allotrope of carbon consisting of single layers of atoms arranged in a honeycomb lattice nanostructure. The name is derived from "graphite," a crystalline form of carbon with its atoms arranged in a hexagonal structure, with the suffix -ene to indicate that the material contains numerous bonds.
The study of graphene grew from experiments with graphite oxide in the mid-19th century. By the mid-20th century, scientists began to theorize about the existence of graphene as a single-layer structure of graphite. Since the early 2000s, scientists have learned a great deal about this material's properties and potential applications.
One such individual is Adrian Nixon, a Chartered Chemist, member of the Royal Society of Chemistry, a Strategic Advisory Board member of the international space transportation association StellarModal, and board member of the International Space Elevator Consortium ISEC (ISEC).
Nixon is also the founder and a board member of Nixene Publishing and the editor of its flagship publication — the Nixene Journal. This journal is an affiliate member of the University of Manchester's Graphene Engineering Innovation Centre (GEIC) — an engineering center that specializes in the rapid development and scaling-up of graphene and other 2D materials.
In March of 2021, Adrian and his colleagues were commissioned by the Foundation for the Future (a bipartisan political action committee) to create a report¹ on the state of graphene for the U.S. Government and policymakers.
As Nixon told Interesting Engineering, graphene was considered an impossible material until a few years ago. In 2004, however, researchers at the University of Manchester isolated graphene for the first time. This led to the field of graphene and 2D materials becoming a reality and for the University of Manchester to become one of the key centers for research.
"The National Graphene Institute (NGI) does the basic scientific research, the Graphene Engineering Innovation Centre (GEIC) does the applied research and turns the science into technology and then helps bridge 'the valley of death' for taking the technology and helping it scale up to become industrially commercial," said Nixon.
Over time, new techniques emerged that can produce single-crystal graphene in sheets centimeters in scale, not just microns. Much of the credit for this goes to Alfonso Reina and his colleagues from MIT, who demonstrated how graphene could be produced using the chemical vapor deposition (CVD) method in 2009.
Since then, the CVD method, which is relatively low-cost and scalable, has developed from a batch process to a continuous industrial process. However, it was not until about a decade later that graphene was considered a possible tether material for a space elevator.
In 2021, Adrian Nixon, Debbie Nelson, and Rob Whieldon had the opportunity to brief NASA on the potential of graphene at the Commercial Space Lecture Series — a weekly teleconference meeting where NASA and representatives from the commercial space community come together to discuss mutual concerns, challenges, and possibilities.
The presentation, titled "Impossible to Industrial in 17 years," showed how graphene had progressed from theory, to the point where it could be mass-produced, in a little over a decade and a half. As they indicated, the techniques for the industrial manufacturing of graphene had increased in both scale and speed².
At present, it has reached the point where kilometer-scale continuous graphene fibers can be produced. And researchers at MIT have developed a continuous roll-to-roll technique that can create large sheets of graphene at a rate of around 6.5 feet (2 meters) per minute. What's more, when made as single-crystal sheets, graphene has a tensile strength of around 130 GPa, or 236 times as strong as steel.
¹Nixon, A., Whieldon, R., and Nelson, D., "Graphene: Manufacturing, Applications and Economic Impact." 1st ed. Manchester: Nixene Publishing (2021).
²Nixon, A. "The graphene and graphite landscape: Indications of unexplored territory." Nixene Journal, Vol. 5, No. 10, 8-19 (2021).
A new vision for space
As noted in a previous article, the potential benefits of a space elevator are numerous and profound. According to a study conducted by the University of Colorado, the cost of sending payloads to space using a Space Elevator could be as little as $113 per lb ($250 per kg). This is five to ten times cheaper than what it costs to send payloads and crews to space today, using modern reusable rockets.
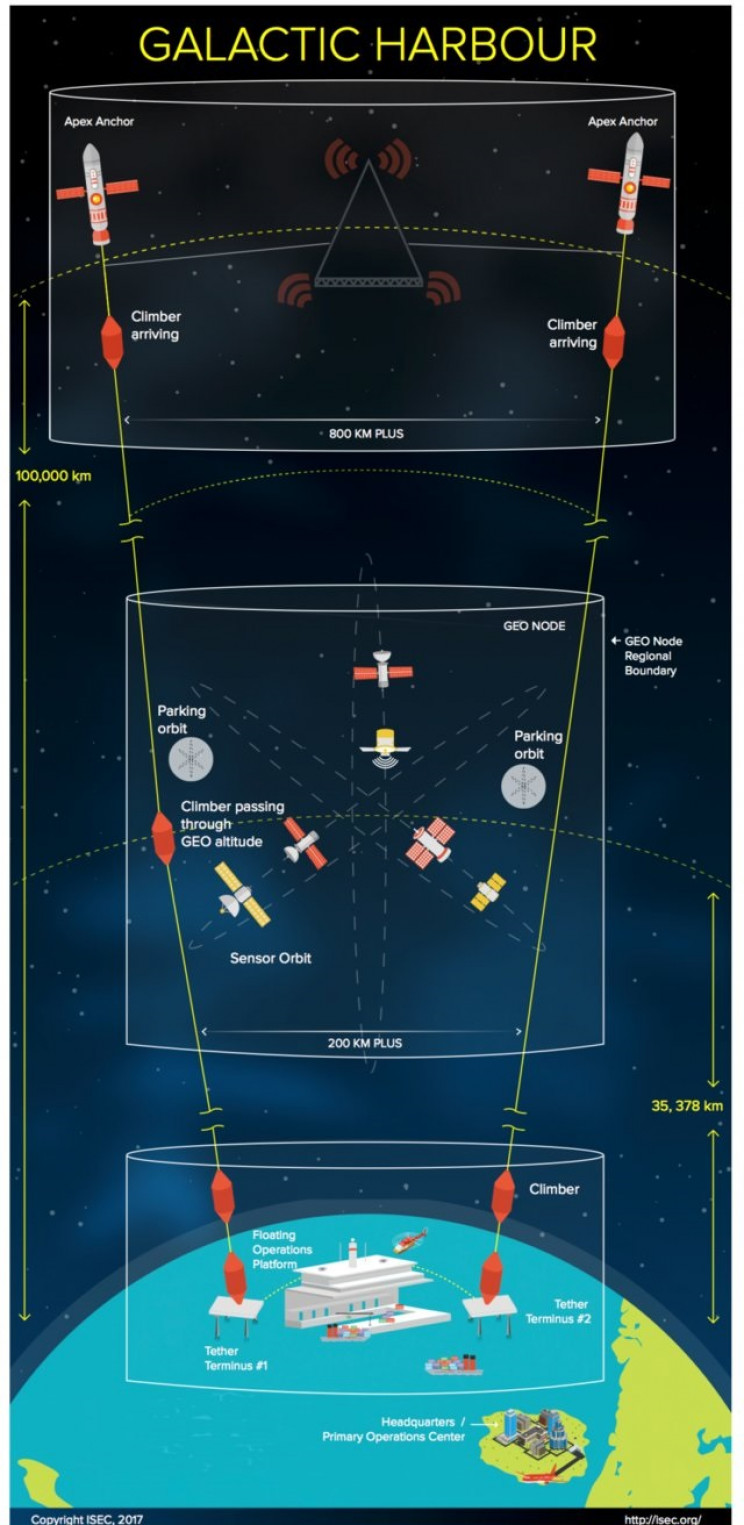
It's also seventy-four times cheaper than what it cost to go to space between 1970 and 2000, using conventional rockets and launch systems. But these benefits increase exponentially when you consider the types of payloads this will allow for, not to mention the environmental benefits of a system that does not rely on chemical propellants.
The overall architecture the ISEC is envisioning (called the "Galactic Harbor") goes beyond the creation of a single Space Elevator, though. According to their 2020 ISEC position paper, titled "Space Elevators are the Transportation Story of 21st Century," their plan is to create a family of six elevators built in pairs in three locations around the planet.
This would include two-elevator Galactic Harbor installations in the Atlantic Ocean, Indian Ocean, and the Pacific Ocean. This architecture also entails the cooperative use of rockets and space elevators to create a space transportation infrastructure that would enable interplanetary travel by the second half of the century.
The details of this architecture were spelled out by Dr. Swan and his colleagues in a 2020 ISEC position paper titled "Space Elevators are the Transportation Story of 21st Century." Among the benefits they cite, a Space Elevator would:
- Enable endless opportunities for commercial enterprises, research, and travel
- Move 170,000 MTs of cargo a year to Geostationary Earth Orbit (GEO) and beyond
- Enable the creation of space stations at GEO, Lagrange Points, and beyond
- Allow for rapid transit to orbit (7.76 km/sec) routinely, safely, and robustly
- Allow fast transit to Mars (minimum of 61 days to 400+ days)
- Allow missions to launch for Mars every day (not just every 26 months)
- Create no rocket exhaust or contribute to global warming
- Not add any additional space debris
The environmentally-friendly aspect of this architecture is paramount. By relying on electricity alone — which can be provided by solar, induction, nuclear, or combination thereof — the Galactic Harbor would be able to place payloads in orbit that would otherwise require dozens (or hundreds) of rocket launches.
With the growth of the commercial space sector and renewed interest in space exploration, countries like the U.S., China, India, and others are hoping to drastically increase the number of launches per year they conduct. Meanwhile, visionaries like Elon Musk and Jeff Bezos are proposing major projects (building a city on Mars, habitats in space, etc.) that would require thousands of launches per year.
A single rocket launch can release up to 300 tons of carbon dioxide into the upper atmosphere, where it can remain for years. While this falls considerably short of passenger flights, which deposited a total of 900 million metric tons into the atmosphere in 2018 alone, scaling up the number of launches conducted every year will increase humanity's carbon footprint considerably.
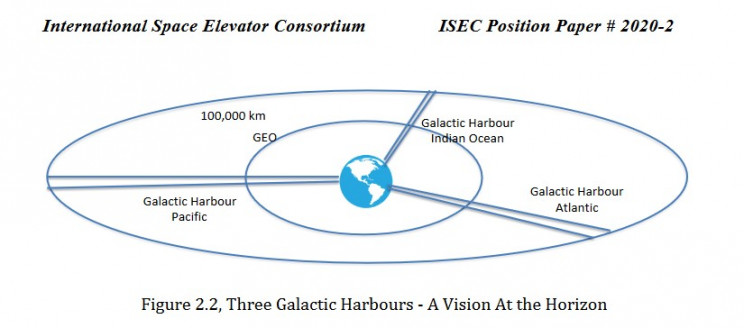
Other "green" aspects of this technology are the way it will practical creation of technology like space-based solar arrays. For some time, scientists have considered this to be one of the most promising means to combat global warming. By being able to lift heavy payloads to orbit for pennies on the dollar and without depositing tons of carbon in the atmosphere, Space Elevators could also help solve the climate crisis.
As for the cost of manufacturing such a megastructure, that may be the most encouraging news of all. Dr. Swan, Nixon, and colleagues estimate it can be done for a very reasonable $18 billion, less than what NASA currently spends annually. What's more, their projections indicate that production could begin before the end of the next decade. Said Dr. Nixon:
"If we push the manufacturing cost assumption down to one cent per square meter, then we come in at $3.6 billion for the manufacture of the tether. Now we have a long way to go to get there, but the experts see the future, the need for space elevators, and the [demand for] transportation infrastructure. As such, this leaves you with $14.4 billion for the rest of the Space Elevator segments."
"One key is that the material prices are falling, and the technology is accelerating towards real production techniques for industrial uses," added Dr. Swan. "This external (from SE) demand is pushing the tether production technologies. We, the SE people, love what is going on and see the material being ready for us in time for an operational date of about 2037."
* * *
There's a reason why interest in the Space Elevator has endured all this time. While it was once thought to be the stuff of science fiction, then a far-off prospect, the day is fast approaching where it will be a feasible possibility. The main stumbling block is now gone with the isolation of graphene and the development of an industrial manufacturing capacity.
Of course, there are still some challenges that stand in the way of realization. As Dr. Swan, Nixon, and Nelson all explained, they can be broken down into three categories. First, there's the issue of scale, as manufacturers still need to develop the capacity to create graphene sheets that are kilometers in length.
Second, there's the issue of speed, where production needs to be ratcheted to several meters per minute (or even per second). Third, there's the issue of quality control, where single-crystal sheets (rather than polycrystalline) of graphene need to be produced, and tests need to be devised to gauge the quality at the nanometer, meter, and kilometer scale.
But compared to the previous hurdles scientists had to deal with, these ones will be entirely surmountable with time. Already, many researchers are working on solutions to these issues. And given the rate at which things are progressing, it shouldn't be long before all the feasibility assessments agree that it can be done.
Then, as the saying goes, "the only thing left to it is to do it!"
Source: https://interestingengineering.com/tech-that-can-make-space-elevators-a-reality
Post a Comment